
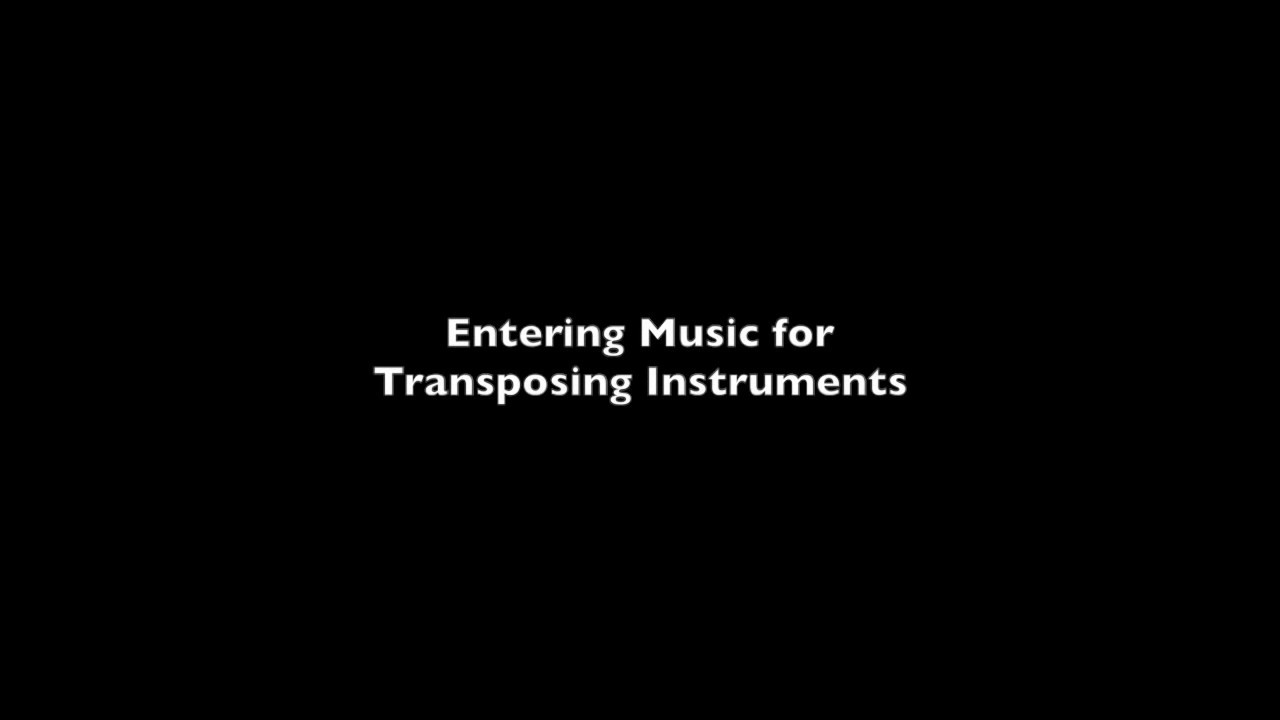

This paper employs analysis of specific SPM PI controllers to provide a more appropriate method for modelling such systems. Due to these errors, the feedback controller often cannot maintain tracking without a high derivative component, which is entirely at odds with experimental observations. However, the details of the operation of the feedback loop have been incorrectly modelled, which results in a decreased stability and an exaggerated ringing at the resonant frequency of the piezoelectric actuator ( z-piezo). Previous work has used control theory to analyse the behaviour of PI and PID feedback loops in the context of SPM, and these models are still being applied in the current literature. Other groups have successfully modelled and implemented proportional-differential controllers, but these are not commonly used. SPM feedback loops usually employ a proportional-integral (PI) controller, equivalent to the common proportional-integral-differential (PID) controller with the differential gain set to zero to avoid amplification of noise. Thus, for reliable SPM operation and analysis the characteristics and behaviour of such feedback loops must be considered. Many well known artefacts can arise from improper feedback settings. Scanning probe microscopy (SPM) imaging relies on feedback loops to maintain a constant interaction between the tip and the sample.
